Peças de reposição impressas em 3D na indústria ferroviária
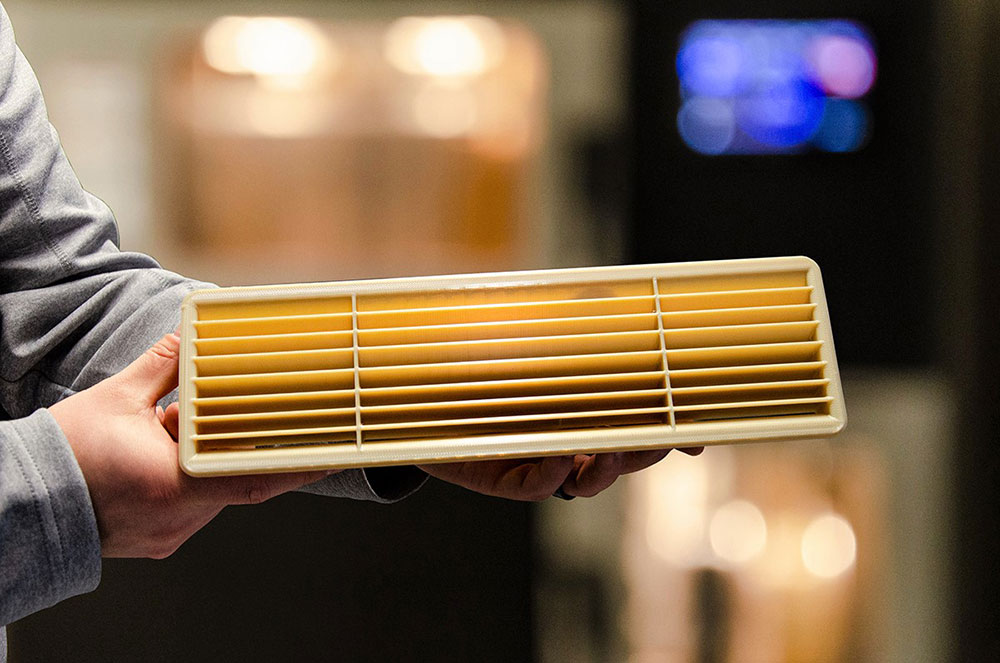
As empresas do setor ferroviário começaram a aproveitar a impressão 3D para o seu negócio. O ciclo de vida dos comboios pode ser de até 30 anos, o que representa um grande desafio para as peças de reposição. Algumas também mudam conforme o desenvolvimento avança, tornando-se um desafio para os métodos tradicionais de fabrico. Peças de reposição para comboios mais recentes costumam estar amplamente disponíveis, mas quando se trata de um comboio com mais de 15 anos, a questão é muito mais complexa. Na maioria dos casos, essas peças de reposição não estão disponíveis ou não existem moldes para a sua produção, tornando o custo de fabrico de peças individuais muito alto e não lucrativo para todos os envolvidos no processo.
A impressão 3D oferece a possibilidade de fabricar peças de reposição individualmente ou em pequenas séries. O processo torna-se assim mais económico, sendo ainda possível fabricar a peça diretamente onde for necessária. Os métodos tradicionais de fabrico de peças de reposição, por exemplo, maquinação e injeção de plástico, são mais caros. Em parte, isso deve-se à quantidade de material desperdiçado durante o processo, à obrigatoriedade de criação de ferramentas para a produção do componente e à necessidade de fazer lotes maiores de uma só vez para manter o custo-benefício.
Ao utilizar a impressão 3D, menos material é desperdiçado. Também não há necessidade de manter grandes quantidades de peças de reposição em armazenamento, uma vez que se pode imprimir, sem qualquer custo adicional, consoante as necessidades. Esta produção por impressão 3D, pode ser efetuada no local, não existindo assim necessidade de esperar que as peças armazenadas em locais distantes sejam enviadas para onde são necessárias.
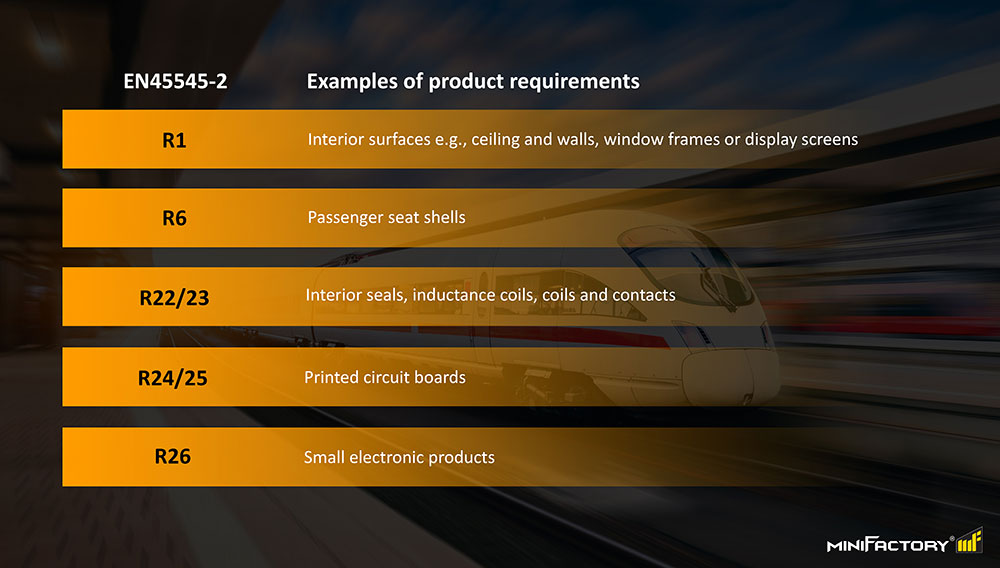
Padronização ferroviária
Mesmo para as peças mais simples, o material em que são produzidas importa. Todos os materiais usados em veículos ferroviários devem seguir a norma EN45545-2. Isso visa atingir o mais alto nível de segurança possível em caso de incêndio. Existe uma grande variedade de materiais que atende ao padrão. Diferentes materiais têm diferentes classificações, ou seja, o material certo é selecionado de acordo com os requisitos da aplicação.
Os veículos ferroviários são classificados de acordo com o nível de risco de incêndio associado ao seu projeto e operação. Os três níveis de risco são: HL1, HL2 e HL3 com HL1 sendo o requisito mais baixo e HL3 sendo o mais alto).
Tecnologia miniFactory, um ajuste perfeito para a indústria ferroviária
A miniFactory trabalha em cooperação com fabricantes de materiais e OEM’s, de forma a encontrar os materiais certos para diferentes aplicações e até mesmo otimizar o processo para materiais específicos. A equipa técnica da miniFactory possuí vários anos de experiência na otimização de processo de fabrico para diferentes tipos de materiais e aplicações. Juntamente com a sua rede de parceiros internacional, cobrindo mais de 25 países, a miniFactory pode garantir uma equipa eficiente e sem esforço para o seu próprio sistema.
A impressora miniFactory Ultra 3D é capaz de imprimir vários materiais diferentes com certificação EN45545-2. Por exemplo, materiais baseados em PA e PC, até materiais de alto desempenho como ULTEM9085 e PEKK. A câmara aquecida de 250˚C da impressora garante um ambiente ideal e consistente para o fabrico de componentes. A tecnologia servo do dispositivo leva à repetibilidade e confiabilidade da tecnologia de fabrico a um nível totalmente novo. Não importa o material, a impressora miniFactory Ultra imprime com a mesma qualidade de sempre.
O software de monitorização de processo AARNI, desenvolvido pela miniFactory, pode ser utilizado no controlo de qualidade e certificação do processo de fabricação de peças de reposição. A uniformidade do processo é a chave para um processo de fabricação confiável e uniformidade das peças. Este é um fator significativo na produção de peças de reposição ferroviárias.
Exemplo de peças de reposição ferroviárias imprimíveis em 3D:
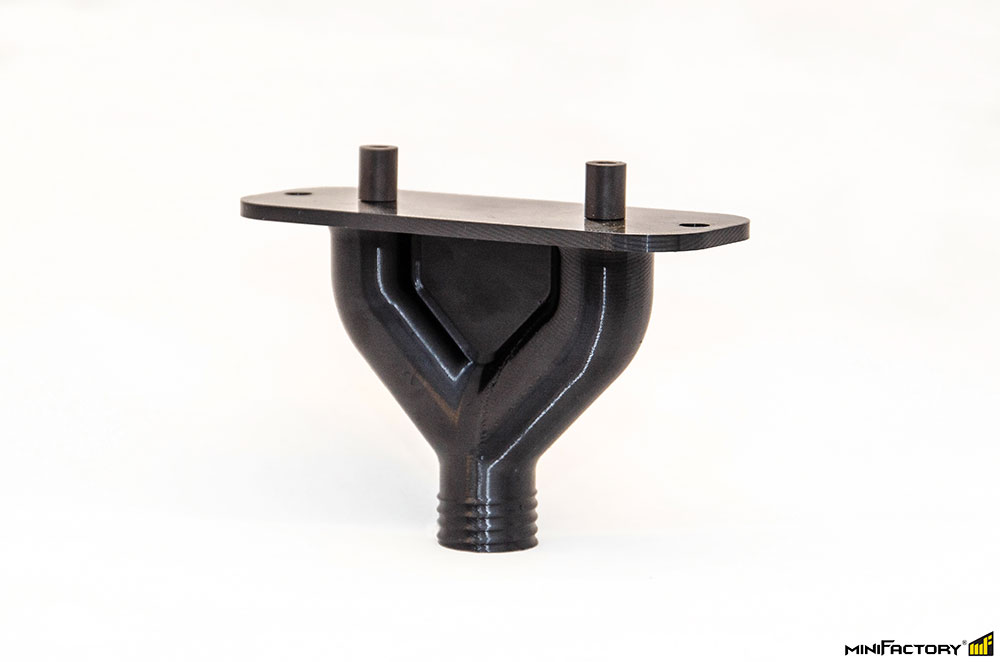
Este suporte de sensor é leve e possuí integração completa, incluindo capa para fios e rosca de fixação. Possui uma geometria complexa que não pode ser fabricada com métodos tradicionais, sem a utilização de moldes complexos. O tamanho da peça é 16 x 11 x 6 cm e o custo por peça é de 25 € em ULTEMTM AM9085F.
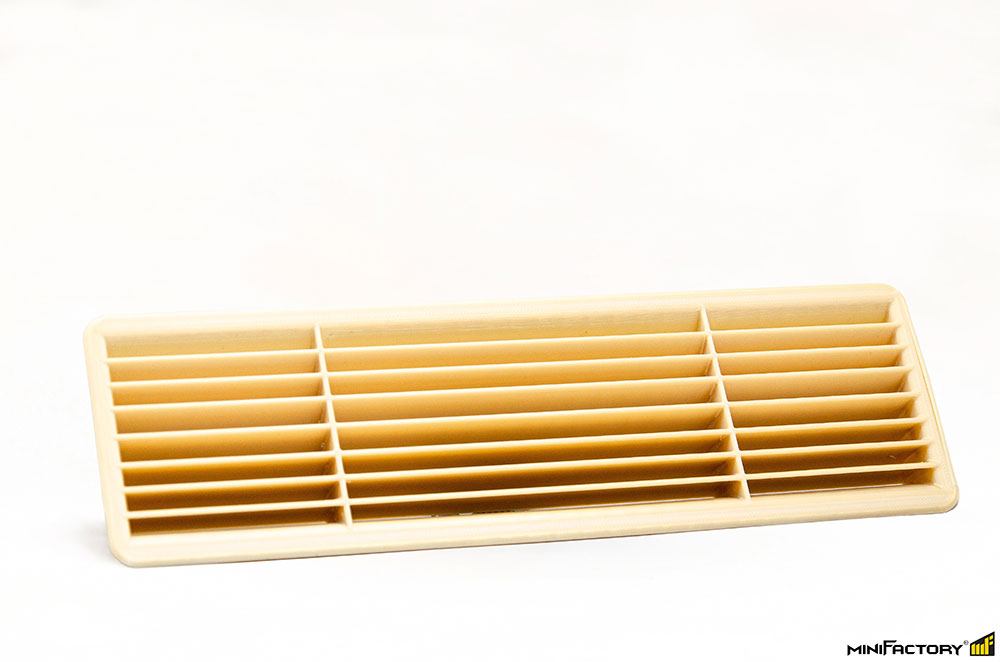
Esta peça de ventilação otimizou o fluxo de ar e o acessório de encaixe rápido. A produção deste componente não é viável através de maquinação CNC, uma vez que uma peça desta dimensão e geometria, produziria grande quantidade de desperdício de material. Com a im-pressão 3D, é possível reduzir os custos significativamente. O tamanho da peça é de 32 x 10 x 3 cm e o custo por peça é 55 € feito com filamento ULTEM TM AM9085F.
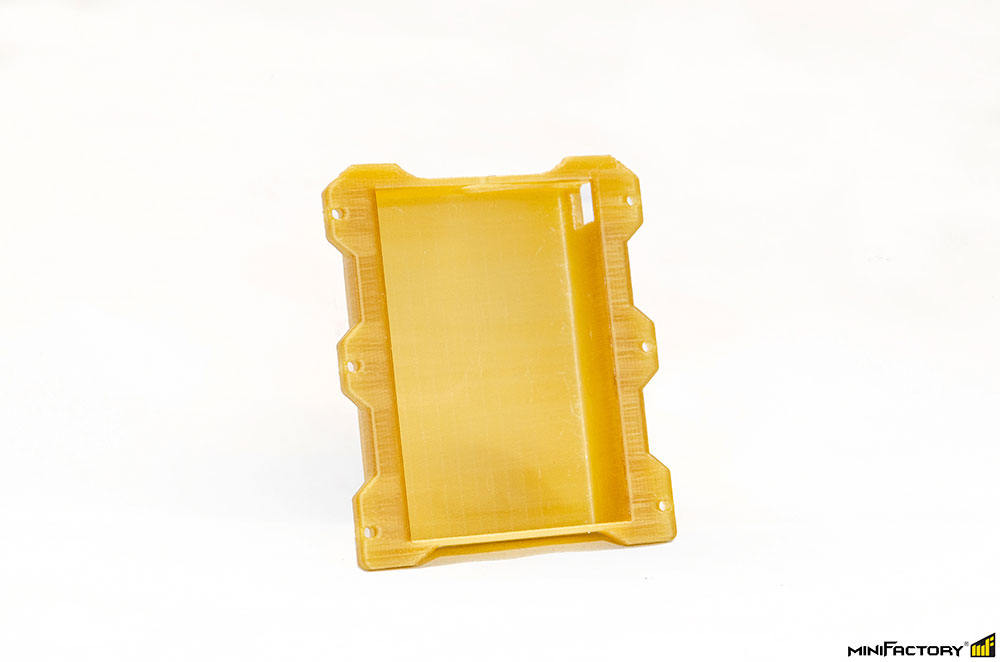
Tampa da bateria em PEKK. PEKK é um material de grau EN45545-2 com propriedades químicas e mecânicas extremamente boas, o que o torna uma boa escolha para esta aplicação. Essa cobertura seria fácil de fabricar com métodos tradicionais. No entanto, com a manufatura aditiva, não há desperdício de material, então o custo por peça é significativamente menor. O tamanho da peça é de 12 x 10 x 3 cm e o custo por peça de 90 € em PEKK-A.